Infrastructure
The Foundry
The Company is located inside Atul Group’s campus of 50000 Sq. Mtr. area with a covered area of 1,50,000 Sq. Mtr. equipped with cutting edge machinery and state-of-the art manufacturing facilities as listed below:
- 6 Nos. induction furnaces ranging from 3 Ton to 300 Kg. giving us flexibility to produce casting of wide variety of critical chemical compositions & weight.
- Alloyed steel including hyper chrome steel & high chrome steel (upto 32% Cr.)
- All grades of C.I. & S.G. Iron
- Austempered Ductile Iron
- 1 No. 5 Ton Electric Arc Furnace for melting critical steel grades with extremely low sulphur, phosphorous and carbon.
- High pressure moulding line & 50 Ton sand plant supplied by DISA with box size: 1300 x 1000 x 350/350 mm.
- No-bake moulding line of 15 Tons/Hr. capacity for large castings.
- Shell core shooter and PLC controlled mixer for making no bake & CO2 core.
- 2 Nos. shot blasting machines of 48” dia rotary table.Further, a centrifugal casting division is also in the pipeline.
- Y type Hanger Shot Blast machine with blast chamber size of 2000 L X 2540 W X 4800 H mm.
Machining facilities
- DOOSAN NHM 8000 4 axis HMC with twin pallets of 1000mm X 800mm
- BFW CHAKRA VMC TWIN PALLET of 600mm X 1000mm
- 4-Axis ‘MAZAK’ HMC H-630N CNC M/c.
- 2 Nos. CNC turning centres.
- 65 Nos. conventional lathe machines for turning, milling & drilling operations.
- SolidCAM & Solidworks for design development and machining.
- Mazak HMC H-630N
- VTL of table size 1.5 Mtrs.
- CMM 2000mm X 1200mm X 1000mm under installation
In-house Laboratory
- The Chemical Lab is fully equipped with two 24-hour online Spectrometers of German Make supported by a fully equipped wet analysis laboratory & carbon silicon analyzer.
- Universal Testing Machine of 40 Ton capacity with computerized interface and graph printing facility.
- Impact Testing Machine of 500 Ton capacity for checking impact strength at -40 °C
- Pull Testing Machine of 500 Ton capacity.
- Fracture Toughness Testing Machine as per ASTMF-604 with facility for conducting test sample at -57 °C.
- Jominy end test as per ASTM to maintain hardenability.
- Micro-processor based microscope with attached camera and related accessories to examine macro and microstructures up to 1000X.
- Hydraulic Press Machine upto 200 Ton capacity.
- TUP Hammer for Draft Gear testing according to the Association of American Railroads specification AARM-901E.
- CMM 2000mm X 1200mm X 1000mm under installation
Heat Treatment facilities
- PLC based operatorless gas fired heat treatment furnace with 4 point temperature control & graph recording facility according to API 6A American Std. (Max. temp. – 1200 °C) of working area 5 mtr. x 1.5 mtr. x 1.5 mtr for air quenching high chrome grinding media.
- PLC based operatorless gas fired heat treatment furnace with 6 point temperature control according to API 6A American Std. (Max. temp. – 1200 °C) of working area 4 mtr. x 2 mtr. x 2 mtr.
- 6 nos. Quenching Furnace of size 3 Mtrs. x 2 Mtrs. with PLC control and quenching facility of 5 Tons load within 45 seconds.
- 3 nos. Water quenching tank from 70,000-2,00,000 Litres with state of art agitation system.
- 2 nos. Electric and 4 nos. gas fired furnaces for tempering with air circulation facility.
- Salt Bath Austenising and Iso-thermal Quenching facility for manufacturing austempered ductile iron.
Hardness Testing facilities
- 4 Nos. Optical Brinell hardness testing machines
- Rockwell hardness testing machine.
- Portable hardness testing machine to check hardness of heavy castings.
Non-Destructive Testing
- Radiographic testing facilities for iridium & cobalt source with site approval from Bhabha Atomic Research Centre, India.
- Radiographic testing and ultrasonic testing machine, magnetic particle inspection requirement, Dye penetrant testing, pressure testing facilities.
Captive Power Plant
- 1 No. 1 MW lean burn GE Waukesha Gas Genset
- 2 Nos. 575 KW lean burn Cummins Gas Gensets
- 2 Nos. 380 KW Cummins Gas Gensets
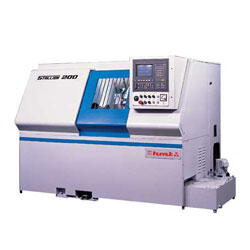
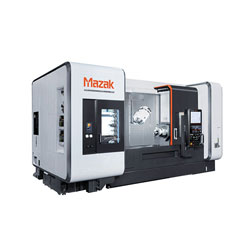
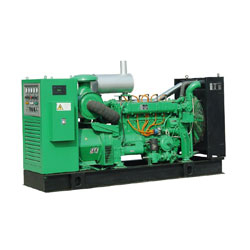
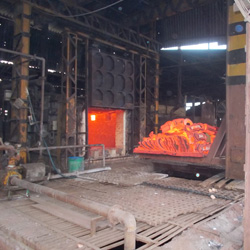
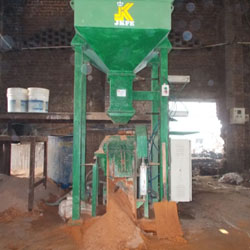
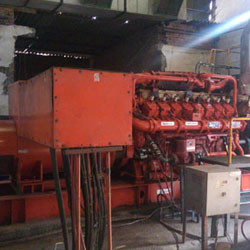